L’Analyse des Modes de Défaillance, de leurs Effets et de leur Criticité est une méthodologie rigoureuse visant à identifier, analyser et atténuer les risques de défaillances d’un produit, d’un processus ou d’un système. Utilisée dans les industries manufacturières, aéronautiques et automobiles, cette approche contribue significativement à l’amélioration de la fiabilité et de la sécurité, tout en réduisant les coûts engendrés par des défauts de conception ou des inefficacités opérationnelles. Son intégration dans la gestion des risques industriels permet une anticipation proactive des problèmes et une optimisation continue des processus.
Table of Contents
Les fondements
L’AMDEC repose sur l’analyse des modes de défaillance possibles d’un système et leur criticité. Cette criticité est mesurée selon trois critères fondamentaux :
- Gravité (G) : impact potentiel de la défaillance sur la performance, la sécurité ou la qualité.
- Occurrence (O) : probabilité d’apparition de la défaillance.
- Détectabilité (D) : capacité à identifier la défaillance avant qu’elle ne génère des conséquences graves.
La criticité est calculée selon la formule : C=G×O×DC = G \times O \times D
Un score élevé indique une nécessité d’actions correctives prioritaires.
Tableau d’évaluation de criticité
Mode de Défaillance | Gravité (G) | Occurrence (O) | Détectabilité (D) | Criticité (C) |
---|---|---|---|---|
Défaillance moteur | 8 | 6 | 5 | 240 |
Défaut d’assemblage | 6 | 7 | 4 | 168 |
Erreur de programmation | 9 | 5 | 6 | 270 |
Défaillance capteur | 7 | 8 | 3 | 168 |
Classification
On distingue principalement trois types d’AMDEC :
- AMDEC Produit : Analyse des défaillances en phase de conception.
- AMDEC Processus : Étude des risques dans la production et la fabrication.
- AMDEC Système ou Équipement : Évaluation des pannes impactant les machines et infrastructures.
La démarche de déploiement
1. Définition du périmètre d’analyse
Déterminer les éléments à analyser et les objectifs de l’AMDEC en fonction des besoins industriels.
2. Constitution d’une équipe interdisciplinaire
Inclure des experts techniques, des qualiticiens et des responsables de production pour garantir une analyse exhaustive.
3. Identification des modes de défaillance
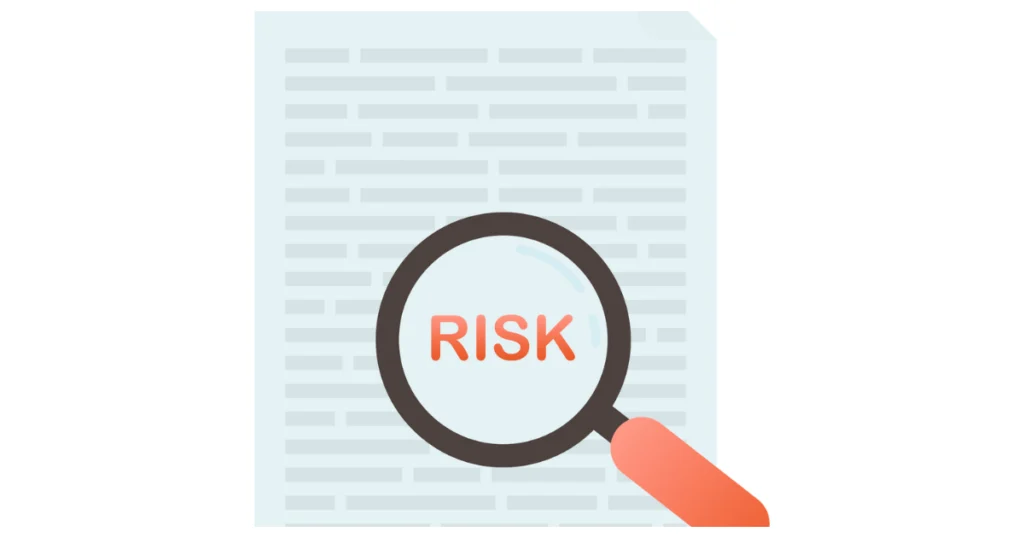
Recenser les sources de défaillance potentielles à partir de données historiques, de simulations et d’observations terrain.
4. Évaluation et hiérarchisation des risques
Attribuer des notes de 1 à 10 à la gravité, l’occurrence et la détectabilité pour déterminer les risques prioritaires.
5. Mise en œuvre des actions correctives
Améliorer la conception, intégrer des contrôles et optimiser les processus pour minimiser les risques identifiés.
6. Suivi et mise à jour continue
Mettre à jour l’AMDEC périodiquement en fonction des évolutions technologiques et des retours d’expérience.
Études de cas
Analyse des Modes de Défaillance, de leurs Effets et de leur Criticité – Usure prématurée des plaquettes de frein
1. Objectif de l’Analyse
Identifier les causes potentielles d’usure prématurée des plaquettes de frein, évaluer leurs effets, leur criticité, et proposer des actions correctives pour réduire les risques.
2. Composants analysés
- Plaquettes de frein
- Disque de frein
- Étrier de frein (caliper)
- Pistons de frein
- Liquide de frein
3. Tableau d’Analyse des Modes de Défaillance, de leurs Effets et de leur Criticité
Composant | Mode de Défaillance | Cause(s) Possible(s) | Effet(s) | Gravité (G) | Occurrence (O) | Détection (D) | Criticité (C = G × O × D) |
---|---|---|---|---|---|---|---|
Plaquettes | Usure asymétrique | Mauvaise qualité des matériaux, montage incorrect | Réduction de l’efficacité du freinage, bruit | 8 | 7 | 3 | 168 |
Plaquettes | Suréchauffement | Freinage intensif (conduite aggressive), disque déformé | Fissures, transfert de matière sur le disque | 9 | 6 | 4 | 216 |
Disque | Rayures profondes | Plaquettes usées jusqu’à la garniture métallique, contamination (poussière, graviers) | Endommagement du disque, vibrations | 7 | 5 | 2 | 70 |
Étrier (Caliper) | Blocage partiel | Corrosion des pistons, accumulation de saleté | Usure accélérée d’un côté, surchauffe locale | 9 | 4 | 5 | 180 |
Liquide de frein | Contamination par humidité | Intervalle de remplacement non respecté, qualité médiocre | Réduction du point d’ébullition, perte d’efficacité du freinage | 8 | 3 | 6 | 144 |
4. Explications détaillées
4.1 Plaquettes de frein
- Usure asymétrique :
- Cause : Matériaux non conformes (friction inhomogène) ou erreur de montage (alignement incorrect).
- Effet : Freinage irrégulier, vibrations et bruit.
- Criticité élevée (168) : Risque de défaillance progressive, mais détectable par des contrôles visuels.
- Suréchauffement :
- Cause : Conduite en descente prolongée ou disque voilé (dissipation thermique insuffisante).
- Effet : Dégradation rapide des plaquettes et du disque.
- Criticité très élevée (216) : Impact direct sur la sécurité.
4.2 Disque de frein
- Rayures profondes :
- Cause : Garniture métallique des plaquettes en contact direct avec le disque.
- Effet : Réduction de la durée de vie du disque et des plaquettes.
- Criticité modérée (70) : Détection difficile sans démontage.
4.3 Étrier de frein
- Blocage partiel :
- Cause : Entretien insuffisant (graissage des pistons non effectué).
- Effet : Usure unilatérale et surchauffe localisée.
- Criticité élevée (180) : Risque de surcharge mécanique.
4.4 Liquide de frein
- Contamination :
- Cause : Absence de remplacement périodique (hygroscopicitée du liquide).
- Effet : Ébullition du liquide en cas de freinage intense.
- Criticité moyenne (144) : Effets indirects mais critiques.
5. Plan d’actions correctives
Priorité | Action | Responsable |
---|---|---|
1 (C=216) | Utiliser des plaquettes en matériaux haute performance (céramique/carbone) | Service Achats |
2 (C=180) | Réviser les procédures d’entretien des étriers (nettoyage/graissage) | Atelier Maintenance |
3 (C=168) | Former les techniciens au montage des plaquettes (utilisation de gabarits) | RH / Formation |
4 (C=144) | Raccourcir les intervalles de remplacement du liquide de frein | Service Clientèle |
6. Surveillance et amélioration continue
- Contrôles qualité :
- Vérification systématique des plaquettes après 10 000 km (épaisseur résiduelle).
- Analyse thermique des disques par caméra infrarouge.
- Retours clients :
- Mise en place d’un système de feedback pour identifier les cas d’usure prématurée.
- Revue :
- Mise à jour annuelle de l’analyse en intégrant les données terrain.
7. Synthèse
L’analyse révèle que les causes principales d’usure prématurée sont liées à la qualité des matériaux, aux pratiques d’entretien, et à la conduite aggressive. Les actions prioritaires ciblent l’amélioration des composants et la formation des acteurs clés pour réduire la criticité globale de 30% sur 12 mois.
FAQ
1. Pourquoi AMDEC est-elle essentielle ?
L’AMDEC permet d’anticiper et de prévenir les défaillances critiques, améliorant ainsi la fiabilité des produits et la sécurité industrielle.
2. Comment choisir entre AMDEC Produit, Processus et Système ?
Le choix dépend de l’objet de l’analyse :
- AMDEC Produit : phase de conception et développement.
- AMDEC Processus : contrôle des procédés de fabrication.
- AMDEC Système : évaluation des équipements et infrastructures.
3. À quelle fréquence mettre à jour une AMDEC ?
Une AMDEC doit être révisée périodiquement, notamment après des incidents critiques ou des évolutions technologiques.
Résumé des points clés
- Méthode systématique pour identifier et réduire les risques industriels.
- Évaluation basée sur la criticité : gravité, occurrence et détectabilité.
- Trois types d’AMDEC : Produit, Processus et Système.
- Approche proactive pour améliorer la fiabilité, la qualité et la performance industrielle.
- Suivi régulier pour garantir l’efficacité des mesures mises en place.
Conclusion
L’Analyse des Modes de Défaillance, de leurs Effets et de leur Criticité est un outil stratégique incontournable pour améliorer la fiabilité industrielle et optimiser la gestion des risques. En permettant une identification proactive des défaillances potentielles, elle contribue à minimiser les interruptions de production, à renforcer la sécurité et à garantir la conformité aux normes de qualité. Son efficacité repose sur une mise en œuvre rigoureuse, incluant une analyse détaillée des processus, un suivi constant des performances et une mise à jour continue pour intégrer les évolutions technologiques et les retours d’expérience terrain. Une adoption méthodique de cette démarche assure une amélioration continue, réduisant ainsi les coûts d’exploitation tout en augmentant la satisfaction client.